Aluminium Casting Defects
Segregation is one of the defects in the casting process When casting an alloy, segregation occurs, whereby the concentration of solute is not constant throughout the casting This can be caused by a variety of processes, which can be classified into two types.
Aluminium casting defects. Die casting is a permanent mould casting where the molten metal fills the mould cavity due to the gravitational force or external pressure The mould cavity is made up using two hardened steel dies which are shaped according to the desired product Die casting generally made of noferrous material like zinc, Tin based alloy, aluminium, copper, etc. RADIOGRAPHIC INDICATIONS FOR CASTINGS Gas porosity or blow holes are caused by accumulated gas or air which is trapped by the metal These discontinuities are usually smoothwalled rounded cavities of a spherical, elongated or flattened shape. Here are the five main types of irregularities found in aluminum castings Shrinkage – Shrinkage defects occur during the solidification process Open shrinkage defects are found on the surface of castings, whereas closed shrinkage defects are formed within the casting, when isolated pools of liquid are allowed to form within the solidified.
The Aluminum Foundry Handbook of Casting Defects was created by Foundrymen for Foundrymen The handbook lists the causes, controls and detection methods for most aluminum casting defects It is a critical tool for supervisors, engineers and quality personnel of aluminum foundries. Aluminum sand casting defects to look out for are residual oxide film, inclusion, core erosion, gas holes and shrinkage porosity Sand cast aluminum components are widely used in the automotive and transportation industries including aerospace Parts commonly produced with sand casting include the powertrain, supports, suspensions, casings, gears and many others. Types 1 Shift or Mismatch The defect caused due to misalignment of upper and lower part of the casting and misplacement of 2 Swell It is the enlargement of the mold cavity because of the molten metal pressure, which results in localised or 3 Blowholes When gases entrapped on the surface.
1) Blowholes Blowholes are smooth, rough holes Blowholes visible on the surface of the casting are called open blows whereas those occurring below the surface of the castings and not visible from the outside are termed as blowholes Blowholes may occur in clusters or there may be one large smooth depression. Metal casting defects are the imperfect conditions of the casting in comparison with the requirement that must be repaired, removed, or rejected Some sand casting defects are small that can be acceptable tolerance, some can easily be repaired and machined Some are severe that have no other way but reject and start another casting batch. Metal mold casting is prone to crack defects, because the metal mold itself has no concession, and the cooling rate is fast, which easily causes the internal stress of the casting to increase If the mold is opened too early or too late, the casting angle is too small or too large, the coating layer is too thin, etc, it is easy to cause.
Type of Failure Procedural Errors Solution Localized shrinkage porosity & Incomplete casting • Using a sprue with a very small diameter • Discrepancy in temperatures between the casting ring/ mold and the molten alloy • Insufficient casting pressure during the casting process • Incomplete elimination of wax and incomplete venting • Higher viscosity of the molten alloy Larger sprue diameter to allow proper flow of molten metal into the mold • Sprue to be attached at the bulkiest. If oxide formation is the cause of your porosity, then your materials will also benefit from being properly degassed after melting or filtered before using the metal for making the casting Hot tears and hot spots are metallurgical defects that occur because of problems during cooling. Defects in castings − The student should be able to diagnose the major defects in castings and propose methods of preventing them Prerequisites − Basic knowledge of physics and foundry practice Date of Issue 1994 EAA European Aluminium Association.
The Aluminum Foundry Handbook of Casting Defects was created by Foundrymen for Foundrymen The handbook lists the causes, controls and detection methods for most aluminum casting defects It is a critical tool for supervisors, engineers and quality personnel of aluminum foundries. Porosity is one of the main defects in castings and is caused by both trapped gases in the molten metal and as the casting shrinks during cooling Shrinkage porosity is by far the most common type and can usually be detected on the surface of a cast part by what appear to be small holes or cracks. Hello Everyone Welcome To AIM AMIE In this Video We have Seen the Different Types Defects in Casting Process, Do Checkout our playlist Related To casting T.
Let's explore what the different kinds of die casting defects are, and how they're caused Not only do defects often cause die cast parts to be rejected, but. The aim of this paper is therefore to highlight the diagnosis different points of view, defect names of aluminum castings poured into metal molds and provide some reflection and detachment on the. Aluminum die casting defects Case by diecast company china with MAX 00T die casting machine ,center furnace , cnc machining,etc.
During the casting process, aluminum castings are prone to internal defects such as looseness, shrinkage, and porosity After these castings with defects are machined, the surface dense layer components are removed to expose the internal tissue defects. Causes of metal casting defects and prevention methods 1 Stoma (bubbles), choking and air pockets Stomatal pores, one of metal casting defects, which are holes that exist on the surface or inside of castings, which are round, oval or irregular Sometimes multiple pores form a pore cluster, and the subcutaneous pores are generally pearshaped. 21 Casting Defects and How to Prevent Them in Your Products 1 Pinholes Pinholes, also sometimes referred to as porosities, are very tiny holes (about 2 mm) usually found in the cope (upper) part of the mold, 2 Subsurface blowhole 3 Open holes 4 Open shrinkage defects 5 Closed shrinkage.
1 Porosity In the process of producing castings by the sand casting machine, the gas does not escape in time before the molten metal is crusted, resulting in holeslike casting defects The inner wall of the pores is smooth, bright or slightly oxidized. The using of channel and coreless induction furnaces may cause defects in the aluminum die casting Aluminum alloys can be fired by fuel oil or natural gas or electric radiation and resistance, so it is very important to choose the furnace Below are the main situations that degradation often results in the melting and casting process. There are defects in the aluminum die casting depending on the channel and coreless induction furnaces used Since these are fired by fuel oil or natural gas or electric radiation and resistance, the choice of the furnace is very important Degradation often results in the melting and casting process in the following situations.
This defect occurs when fluidity of molten metal is high When mould is porous and does not enough stronger to resist molten metal, this defect occur The liquid metal penetrates the mould and mix with sand This gives uneven casting surface. Incomplete casting is common casting defect it occur when molten metal is unable to fill the extremist of the mold and its also called partially complete casting Causes Insufficient alloy is used;. A Some forms of delaminations in lowalloy aluminum are traceable to hydrogen pickup (blisters), extra large grain size, casting defects, and surfacetocenter "smearing" (where lubricant can cause more rapid metal flow than center) The last problem may occur in hammer forging, but is unlikely in press forgings.
Sand Casting Defects Aluminium Casting Defects Steel Casting Defects Sand Casting Defects Open Blows and Blow Holes Blow holes are bubbles of gas entrapped inside the casting Both are caused by gases carried Pin Hole Porosity Hydrogen is responsible for causing pin hole porosity The. The casting surface shows either a step or shallow indentation along the path of incipient mold failure, often with a short metal in presenting the original crack This surface fissure or line defect is known as rattails and it appears as an irregular line across the surface of a castings. Here, the resistance of the structure weakens, and it is more difficult to spot them Significant types of internal defects are Shrinkage defects like macro shrinkage and layer porosity Gas related defects like hydrogen porosity and air entrapment porosity Filling related defects like cold joint and lamination.
Since repairing bad castings can be expensive, it’s important to avoid defect occurrences if possible We’ll look at some common to areas of die casting defects — including wall thickness and die surface porosity — their causes, and how to avoid them You Can’t Correct and Control Defects if You Can’t Measure and Report Them. Coating inside out is considered a serious defect for three piece cans and for two piece cans, if the metal is exposed to a corrosive product, otherwise coating inside out is considered a minor defect for two piece cans. Keywords aluminum alloys, casting defects, casting imperfections, casting defects classification, quality, permanent mold Introduction The final properties and inservice behavior of.
Cracks are often associated with defects such as shrinkage and slag inclusion It usually occurs at the inside of the sharp corner of the casting, where the thick and thin sections meet, and the hot junction area where the pouring riser is connected to the casting. Some other minor casting defects are drops, crushes, cuts and washes Drop occurs when the upper surface of mould cracks and pieces of sand fall into the molten metal Drop may occur due to low green strength, low mould hardness, using hot sand, insufficient reinforcement Defects Resulting from Incomplete Feeding. Pouring metal defects can, for the most part, be avoided by ensuring the molten metal stays warm enough to completely conform to the inside of the mold The gating system can be redesigned to transport the molten metal faster, or to avoid sections that are thin enough to solidify before the metal can fill larger cavities beyond them.
It is a kind of cavities defects, which is divided into pinhole and subsurface blowhole Pinhole is very tiny or small hole and subsurface blowhole only can be seen after machining When gases entrapped by solidifying metal on the surface of the casting , which result in a rounded or oval blowhole as a cavity. Probably caused by an uneven primary coat thickness, giving rise to variable rates of drying 2. In die casting, it is not simple to identify the causes that generate a micro or a macro defect The formation of a coldshut, a missing filling or a critical surface imperfection can often derive from a series of process contributing factors that, if identified, allow determining the most opportune corrective interventions.
Aluminum castings have played an integral role in the growth of the aluminum industry since its inception in the late 19th century The first commercial aluminum products were castings, such as cooking utensils and decorative parts, which exploited the novelty and utility of the new metal. These are akin to shrinkage cavities but are more ribbonlike voids in the metal caused by rapid shrinkage Castings with hot tears or cracks will underperform mechanically Cooling deformation is a common defect in very long, thin castings, but can happen in other shapes too In this defect, the metal casting warps away from its intended shape during cooling, causing it to be outside of specified tolerances. Here are the five main types of irregularities found in aluminium castings Shrinkage – Shrinkage defects occur during the solidification process Open shrinkage defects are found on the surface of castings, whereas closed shrinkage defects are formed within the casting, when isolated pools of liquid are allowed to form within the solidified metal.
Metal Casting Defects Explained Metal casting is a complicated science;. There are a plethora of different ways that it can go wrong at every corner At MRT, we’re committed to quality Our quality management system is accredited to ISO and are approved suppliers to many of the world’s leading electronics, aerospace, medical and. Since repairing bad castings can be expensive, it’s important to avoid defect occurrences if possible We’ll look at some common to areas of die casting defects — including wall thickness and die surface porosity — their causes, and how to avoid them You Can’t Correct and Control Defects if You Can’t Measure and Report Them.
Appearance of Defect Linear indication of metal not joined at time of two metal streams meeting Probable Cause 1 Low metal pouring temperature 2 Poor pouring practice 3 Improper gating 4 Low shell permeability 5 Heavy oxidation of metal increasing surface tension 6 Low metal fluidity Suggested Cure 1 Increase metal and/or mold temperature 2. A weld joint is considered a serious metal plate defect when packed with a corrosive product, when there are gaps in the continuous weld such as in spot welds or when the weld is weakened to the point that it fails under finger pressure Description An obvious, black line (joint) approximately 5 mm (3/16") wide running across the can end or body. 10 Shrinkage Depression This defect is also a type of shrinkage defect, which looks like depressed region on the surface of metal castings This defect is not serious as shrinkage cavity, but still cause poor surface quality and may have some inside defects, so foundries should try their best to solve or improve it.
In die casting, it is not simple to identify the causes that generate a micro or a macro defect The formation of a coldshut, a missing filling or a critical surface imperfection can often derive from a series of process contributing factors that, if identified, allow determining the most opportune corrective interventions. Metal mold casting is prone to have crack defects, because the metal mold itself does not have concealing ability, the cooling speed is quick, it easily leads to increased internal stress of the casting The opening type is too early or too late, the pouring angle is too small or too large, the coating layer is too thin, etc also caused the cracks. Aluminum sand casting defects to look out for are residual oxide film, inclusion, core erosion, gas holes and shrinkage porosity Sand cast aluminum components are widely used in the automotive and transportation industries including aerospace Parts commonly produced with sand casting include the powertrain, supports, suspensions, casings.
RADIOGRAPHIC INDICATIONS FOR CASTINGS Gas porosity or blow holes are caused by accumulated gas or air which is trapped by the metal These discontinuities are usually smoothwalled rounded cavities of a spherical, elongated or flattened shape. These defects can be caused by cold dies, low metal temperature, dirty metal, lack of venting, or too much lubricant Other possible defects are gas porosity, shrinkage porosity, hot tears, and flow marks Flow marks are marks left on the surface of the casting due to poor gating, sharp corners, or excessive lubricant. High viscosity of fused metal or metal is not so hot and so metal is not able to enter thin parts of mold Casting pressure is low.
Aim of the current study is to study defects of an aluminum alloy casting and to improve the quality of casting using quality control tools This study shows the systematic approach to find the root cause of a major defects in aluminium castings using defect diagnostic approach as well as cause and effect diagram. The cause of metal casting defects depends on the components and how they are cast A variety of irregularities can affect metal castings The most common defect is porosity Porosity refers to the voids—the empty spaces—on or within what should be a solid metal casting The cavities in porous metal castings will cause leaking, plating. Aluminum die casting manufacturing were used for many industries over yearsTherefore,control of die casting defects are important for factories info@prodiecastingcom IATF certified.
Defects in casting observed In order to identify the casting defect, the study is aimed in the research work The main objective of the current paper is finding different defects in aluminumalloy die casting and providing their remedies with their causes In this paper casting defects are critically discussed. Appearance of Defect Island of surplus metal on surface of casting, often associated with flash at the casting edge Probable Cause 1 Cracking of primary coat allowing backup slurry to penetrate between pattern and the primary coat faces;. ADVERTISEMENTS Some of the casting defects are described below 1 Surface Roughness Too coarse a moulding sand or when pouring temperature is high leads to rough or pebbly surfaces on castings In steel castings, roughness is produced due to occurrence of surface reaction at mouldmetal interface in which iron is oxidised and iron oxide reacts.
Using Pareto chart major defects in the aluminium castings were noted The major defects for the rejections during production were identified as shrinkages, inclusions, porosity/gas holes and cracks Each defect is studied thoroughly and the possible causes for the defects are shown in Fishbone Diagrams (Cause Effect Diagrams). Aluminium and aluminum alloy billets surface defects Segregation Segregation defects causes and solutions Segregation In the semicontinuous casting process, the knob generated on the surface of the ingot are called segregation Segregation is one of the defects in the casting process When casting an alloy, segregation occurs, whereby the. Aluminum castings have played an integral role in the growth of the aluminum industry since its inception in the late 19th century The first commercial aluminum products were castings, such as cooking utensils and decorative parts, which exploited the novelty and utility of the new metal.
Aluminum Alloy Casting Defects admin June 9, Blog 0 Comments In the process of aluminum alloy casting, it is inevitable that various defects will appear due to improper casting, and the defects must be dealt with in a timely manner. As metal is heated it expands and as it cools it contracts again If this expansion and contraction is not correctly managed, defects can occur in your casting Shrinkage in castings can manifest itself in a number of different ways Shrinkage defects can be placed into 2 categories, open shrinkage defects and closed shrinkage defects.
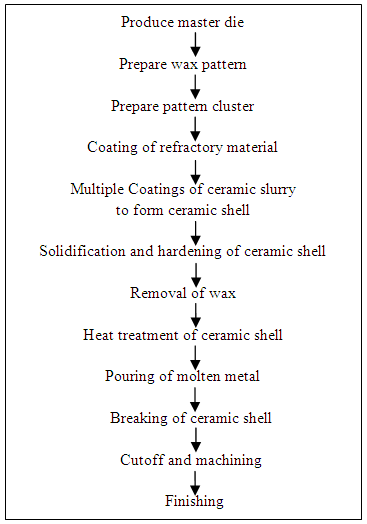
Minimization Of Investment Casting Defects By Using Computer Simulation A Case Study
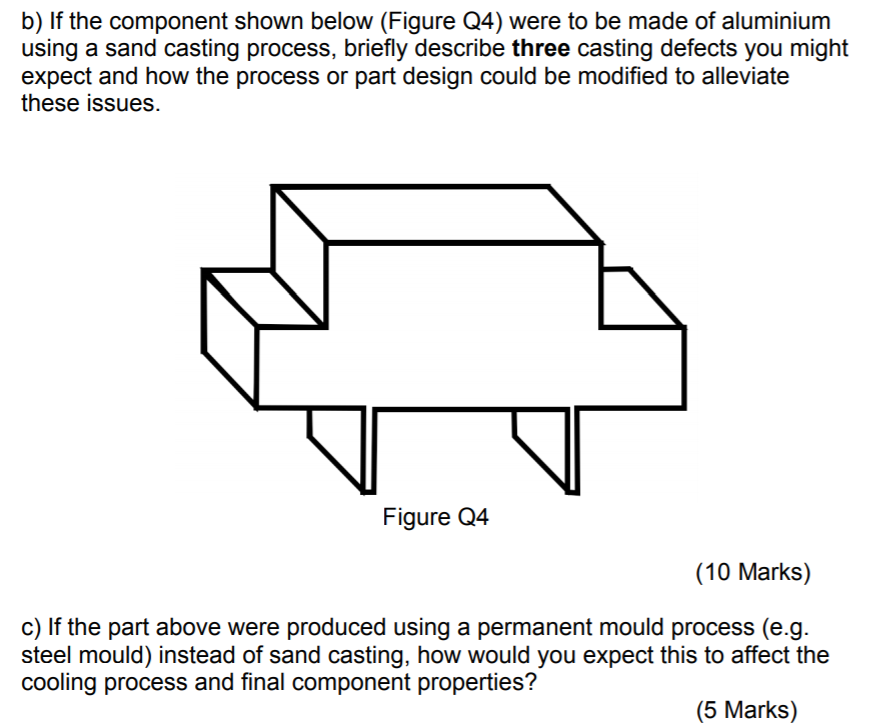
Solved B If The Component Shown Below Figure Q4 Were T Chegg Com
What Is Porosity In Aluminium Sand Casting Haworth Castings Uk Aluminium Sand Castings And Gravity Die Castings Foundry
Aluminium Casting Defects のギャラリー

Blistering In Semi Solid Die Casting Of Aluminium Alloys And Its Avoidance Sciencedirect
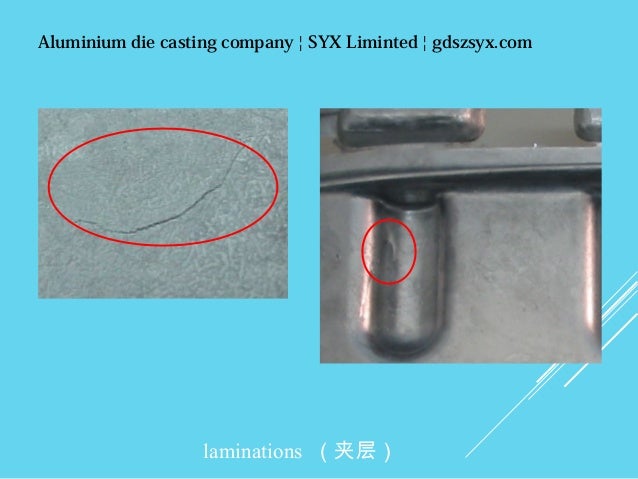
Aluminum Die Casting Defects
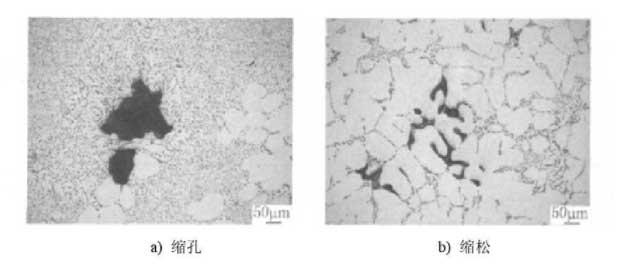
Formation Mechanism Of Shrinkage Cavity And Porosity In Aluminum Alloy Low Pressure Casting Zhy Casting
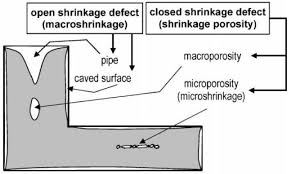
21 Casting Defects And How To Prevent Them In Your Products

Die Casting Defects Filing Solidification Distortion Cavity Fill Filling Thermal Analysis Passage Software

Aluminum Die Casting Defects And Remedies

How To Avoid Aluminum Die Casting Defects Investment Casting
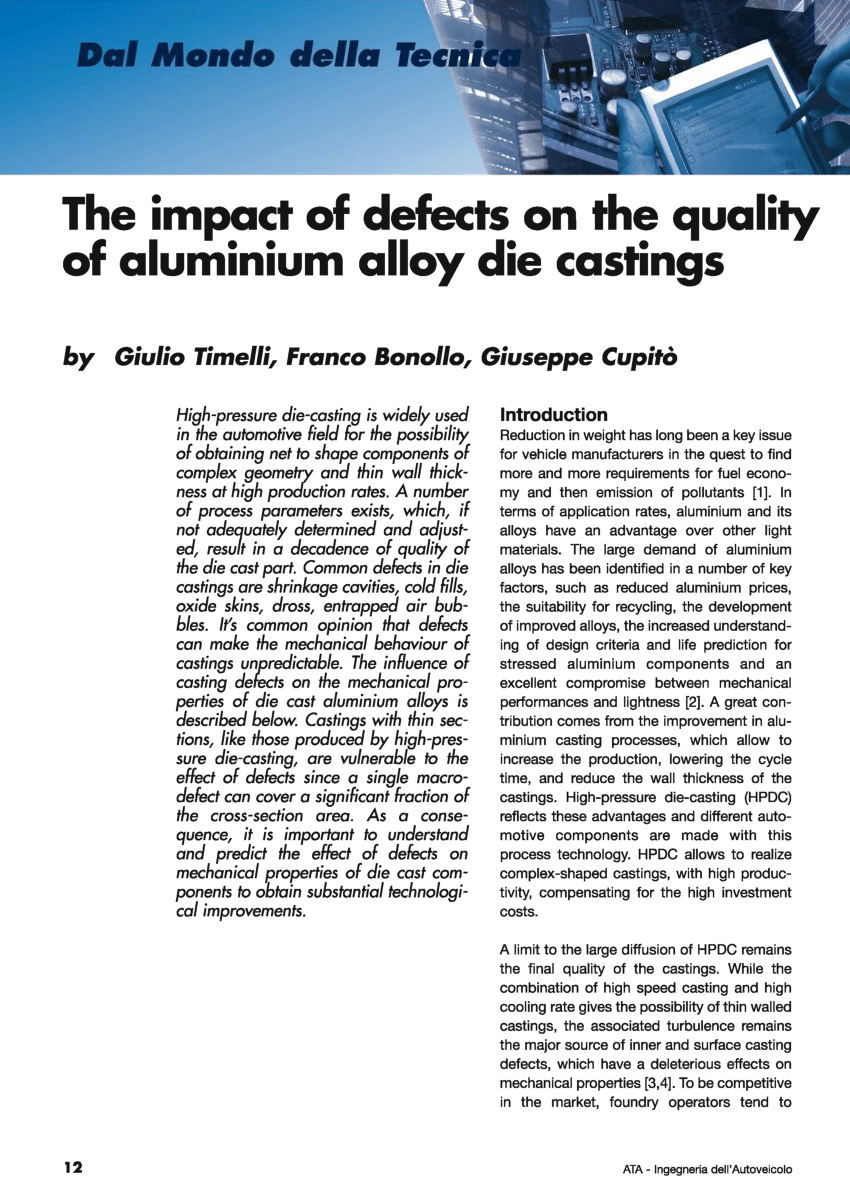
Pdf The Impact Of Defects On The Quality Of Aluminium Alloy Die Castings
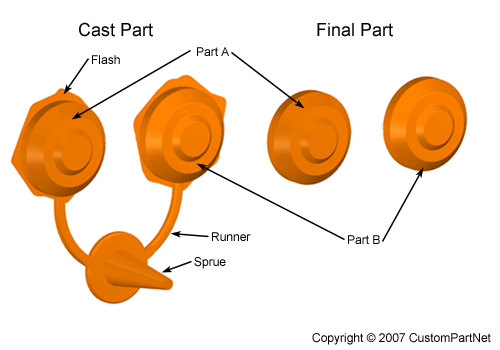
Die Casting Process Defects Design

Casting Defect Wikipedia

Die Casting Defects Causes And Troubleshooting Eco Diecasting
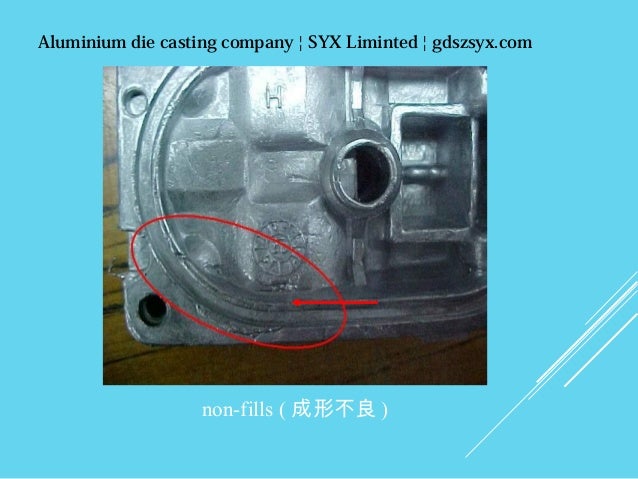
Aluminum Die Casting Defects
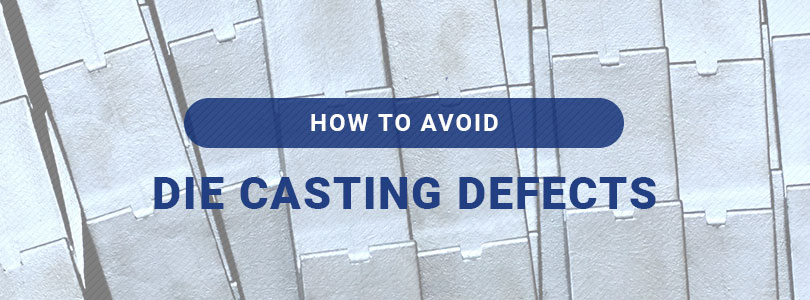
Die Casting Defects How To Avoid Die Casting Defects
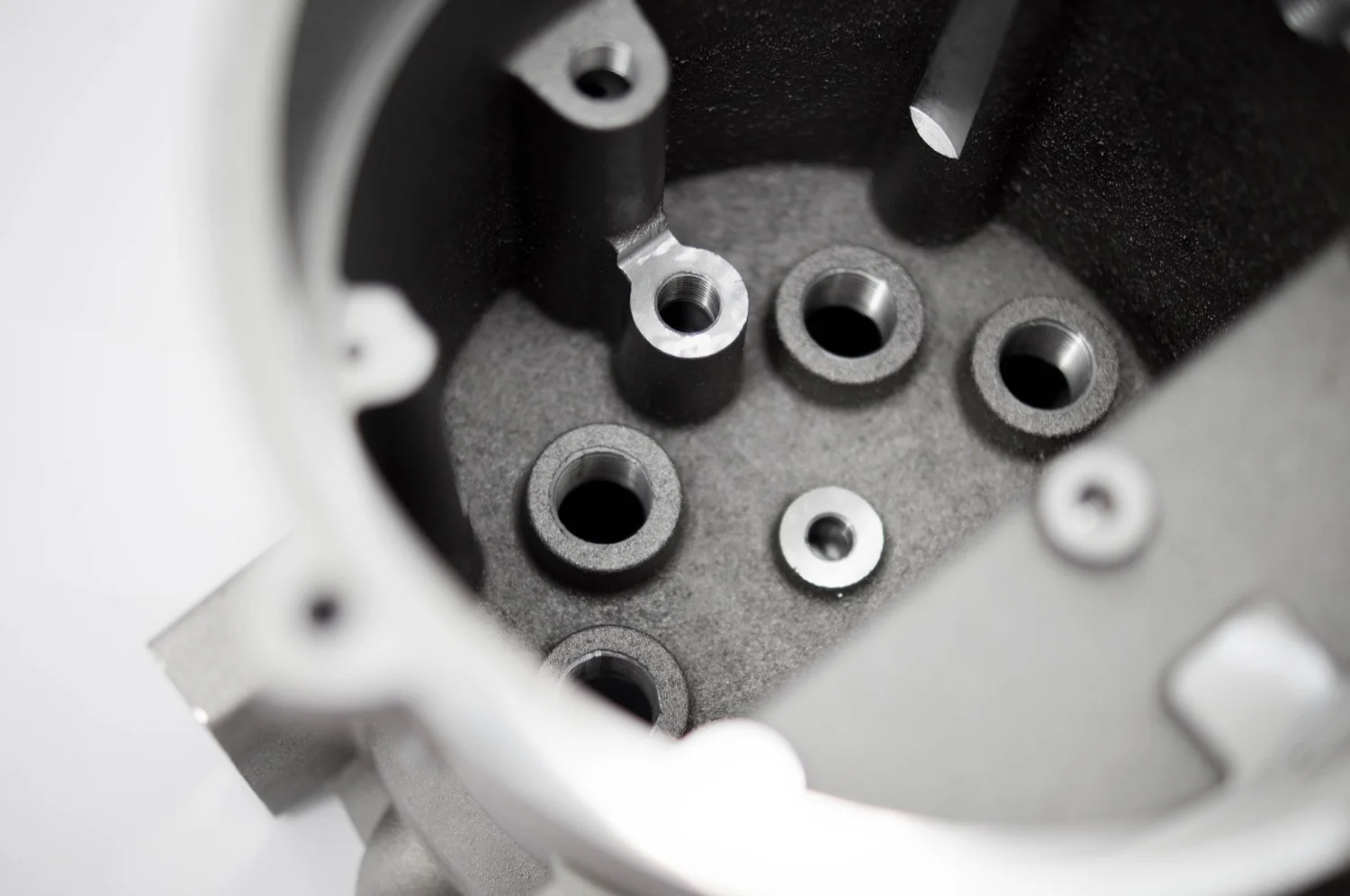
Casting Defects And How To Prevent Them Part 1 Haworth Castings Uk Aluminium Sand Castings And Gravity Die Castings Foundry

Different Types Of Casting Defects And Remedies Studentlesson

Part 2 Die Casting Defects Where Do They Come From Youtube
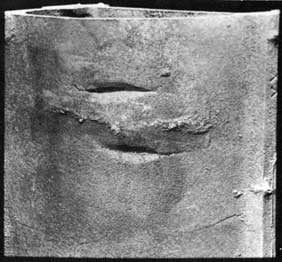
21 Casting Defects And How To Prevent Them In Your Products

Microstructure Of Aluminum Casting Alloy 443 Al 5 Si A Alloy 443 F Download Scientific Diagram
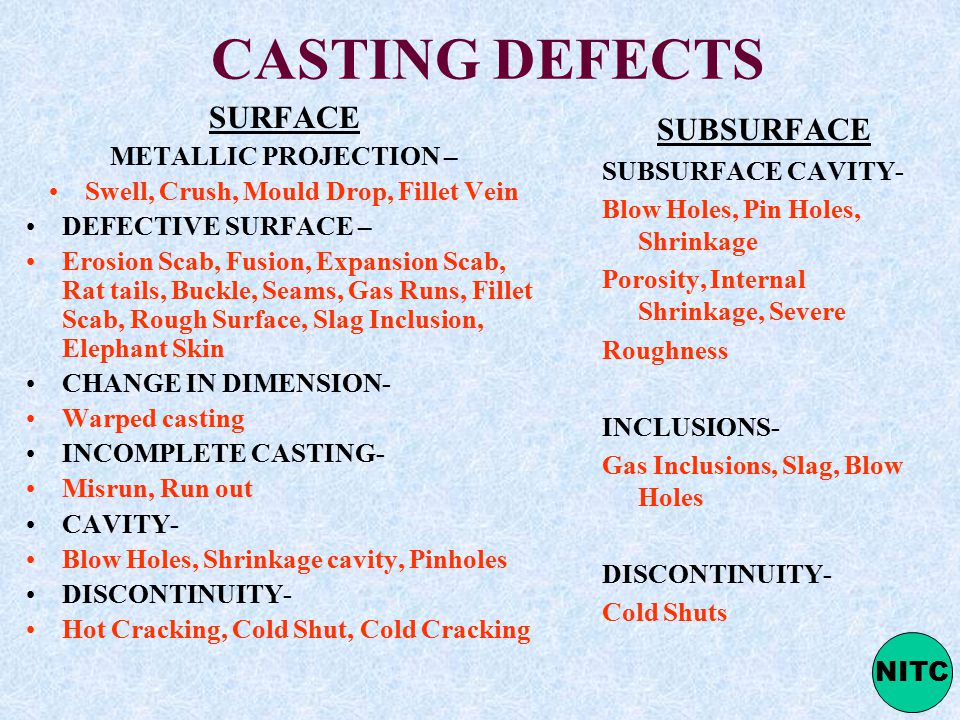
Casting Defects Metal Casters Try To Produce Perfect Castings Ppt Video Online Download

Solutions Fonderie Services Metallurgiques Inc

Metal Foundry Die Casting News Hill And Griffith Company
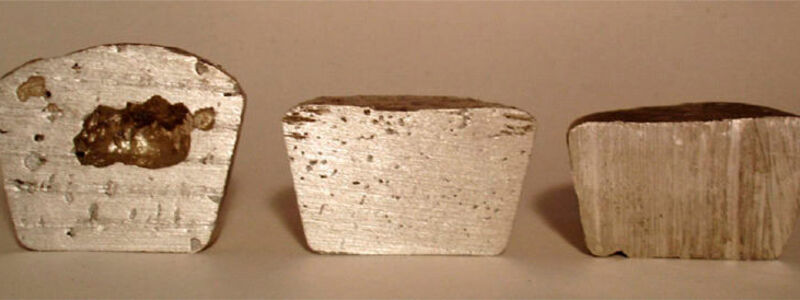
Aluminum Sand Casting

Aluminum Die Casting Defects
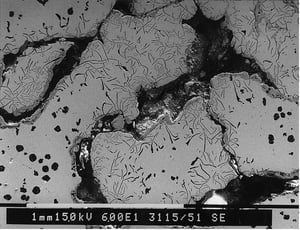
21 Casting Defects And How To Prevent Them In Your Products
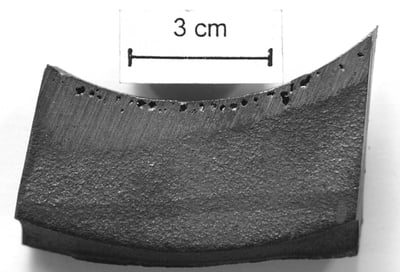
21 Casting Defects And How To Prevent Them In Your Products

What Is Casting Defects Types Causes And Remedies Mechanical Booster

Aluminum Die Casting Defects Case By Diecast Company
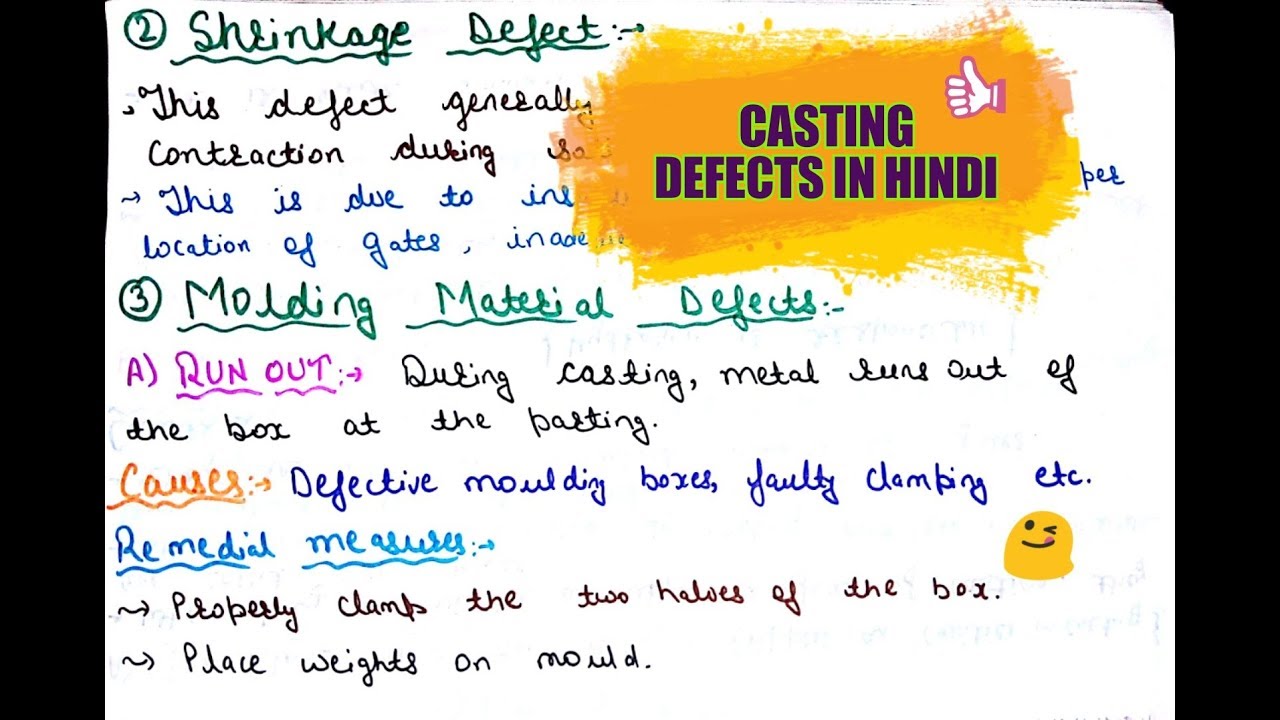
10 Casting Defects In Hindi Material Science Er Ashish Youtube
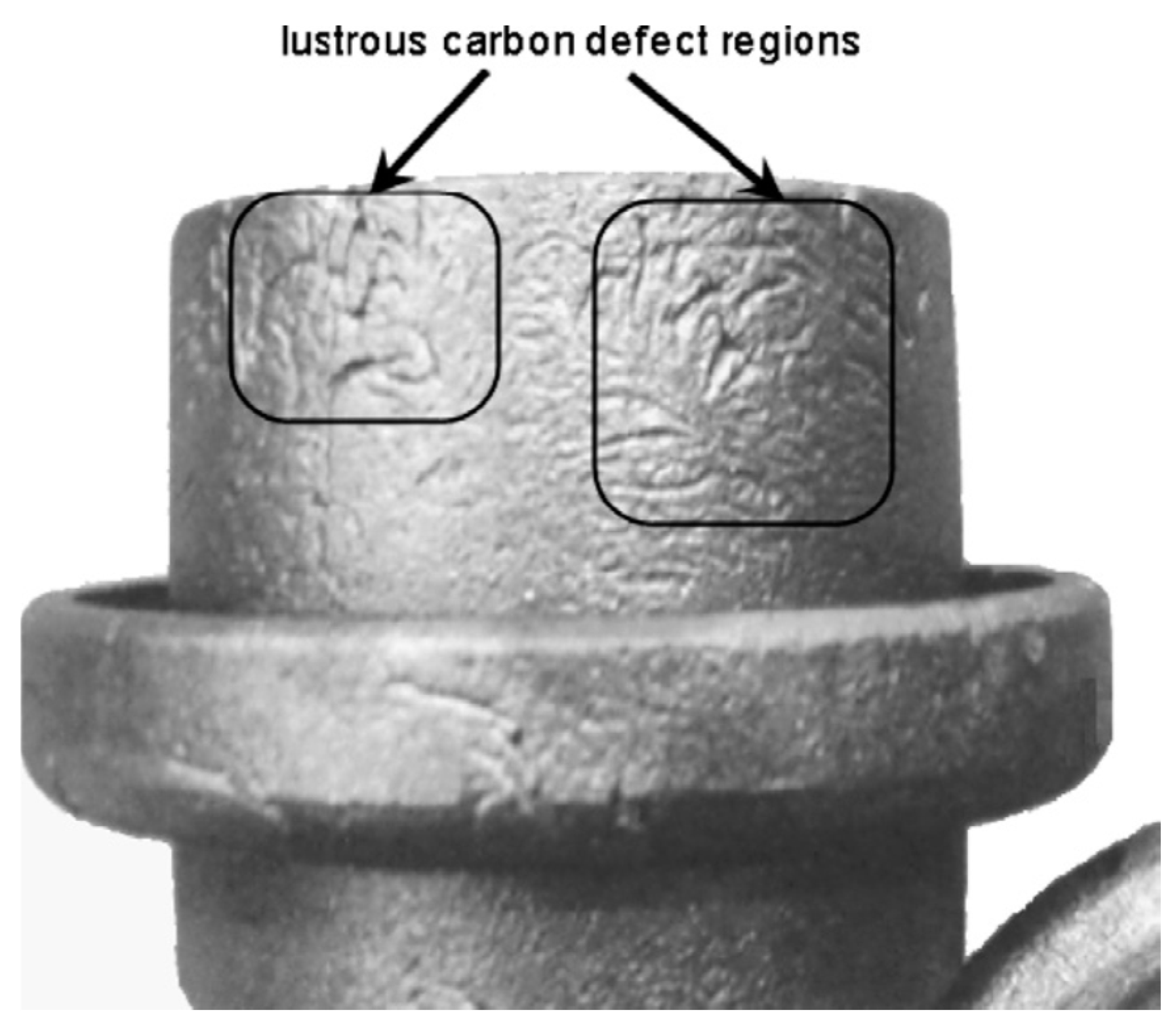
Metals Free Full Text The Impact Of Process Factors On Creating Defects Mainly Lustrous Carbon During The Production Of Ductile Iron Using The Lost Foam Casting Lfc Method Html

Radiograph Interpretation Castings
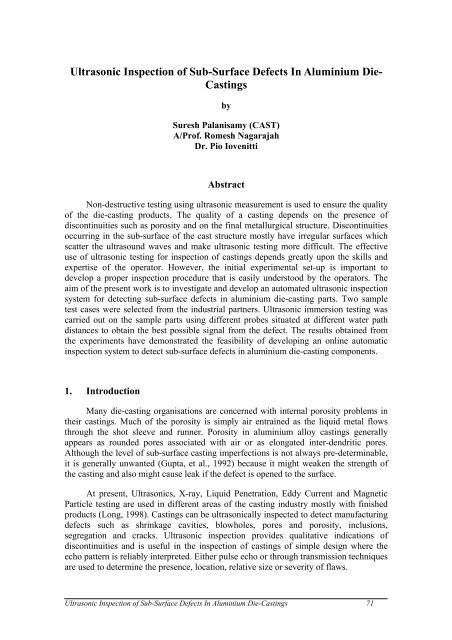
Ultrasonic Inspection Of Sub Surface Defects In Aluminium Die Casting
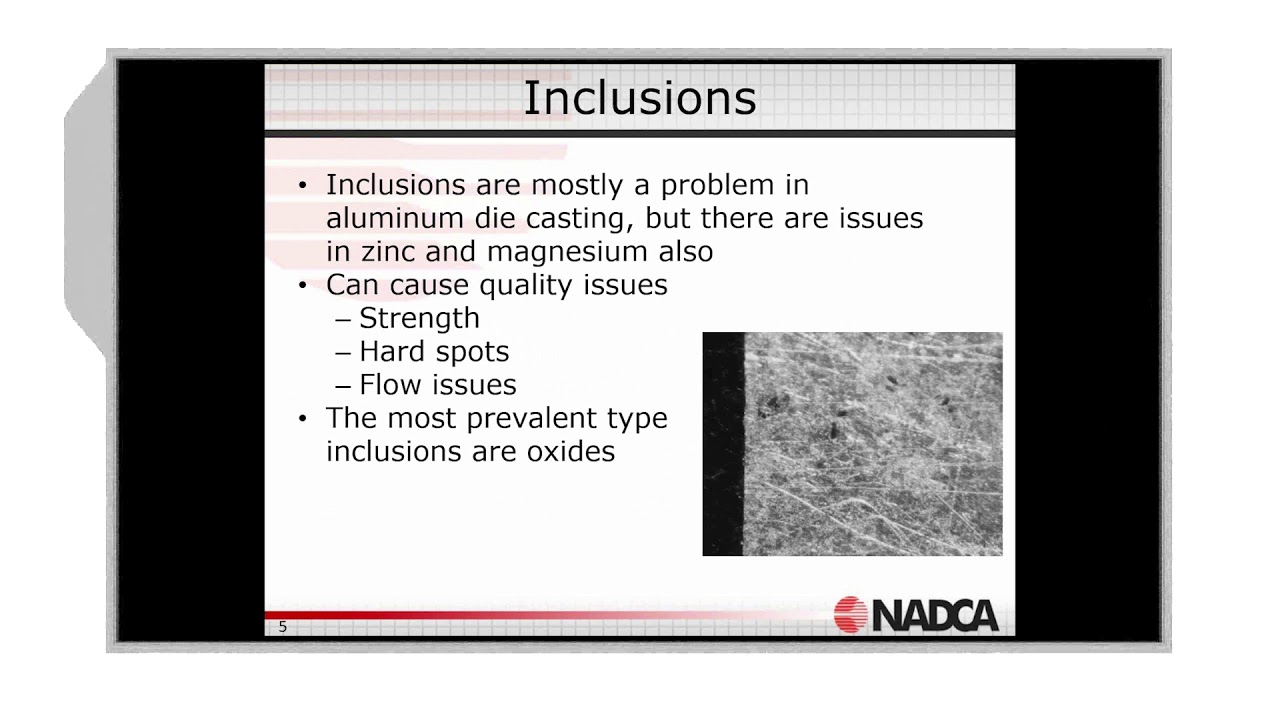
Nadca Video News Die Casting Defects Inclusions Leakers And Cracks
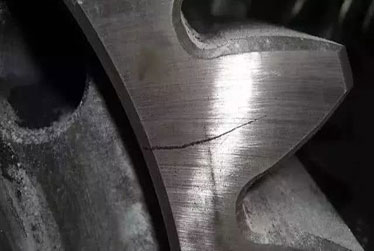
How To Deal With The Surface Defects Of Aluminum Die Casting Emp Tech Co Ltd
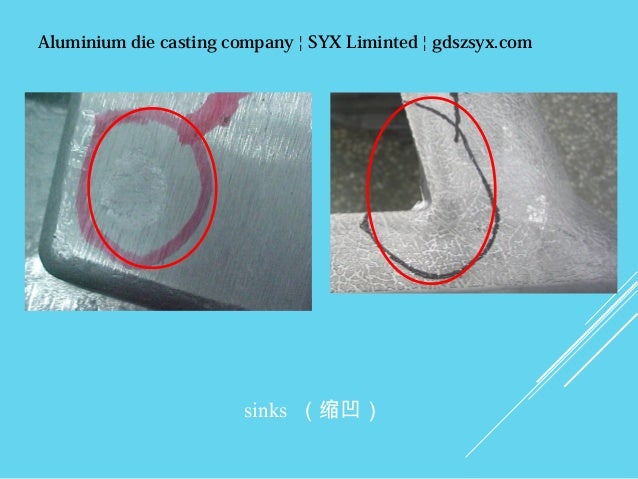
Aluminum Die Casting Defects
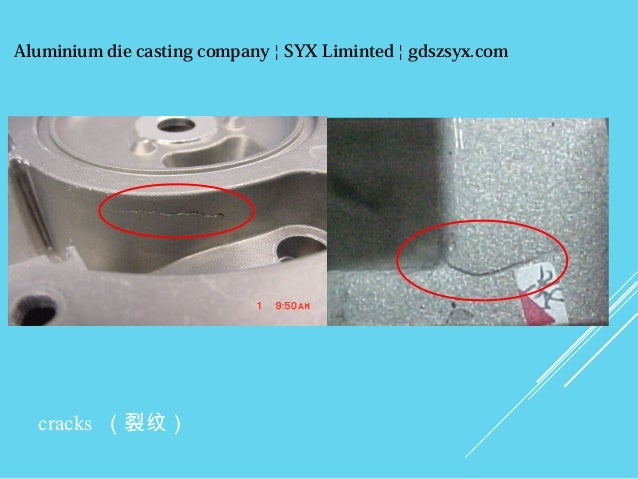
Aluminum Die Casting Defects
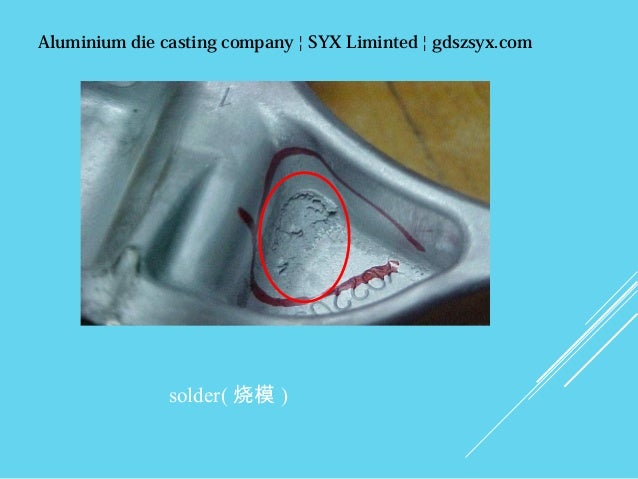
Aluminum Die Casting Defects

Light Alloys From Traditional To Innovative Technologies Intechopen

Defects In Investment Casting Part 1 Uk Investment Casting
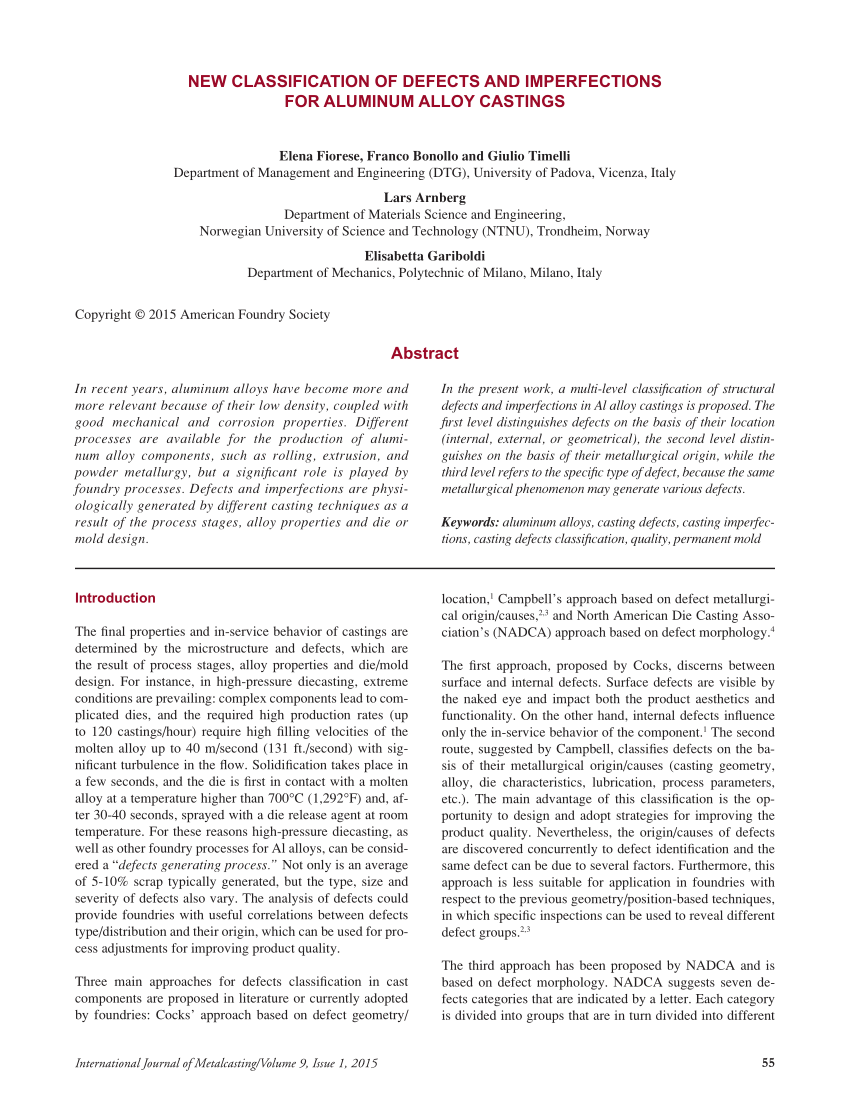
Pdf New Classification Of Defects And Imperfections For Aluminum Alloy Castings
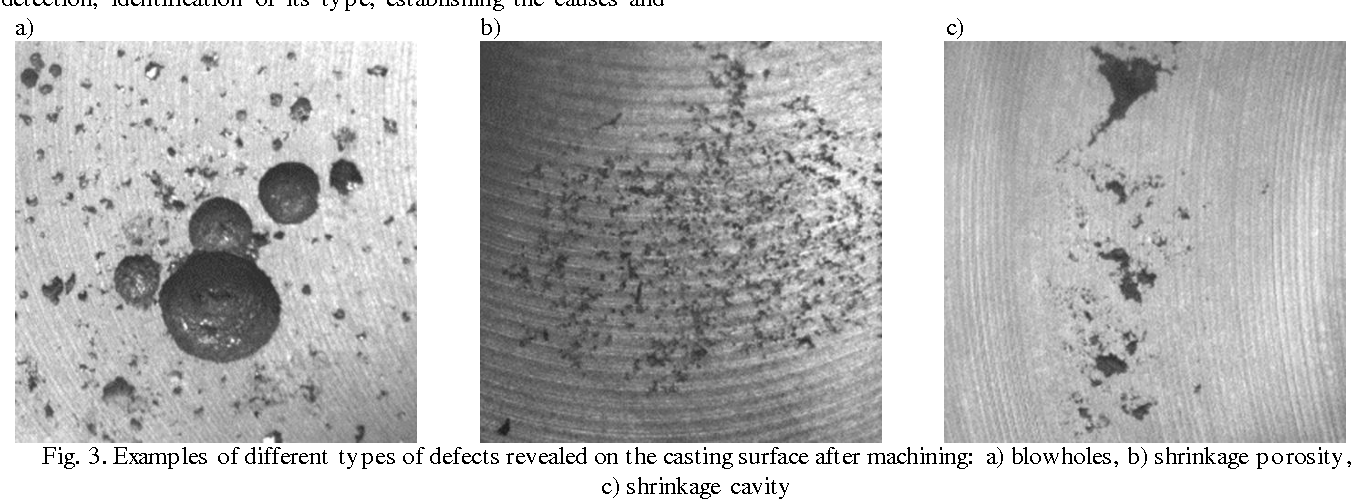
Pdf Automatic Inspection Of Surface Defects In Die Castings After Machining Semantic Scholar

What Is Casting Defects Types Causes And Remedies Mechanical Booster
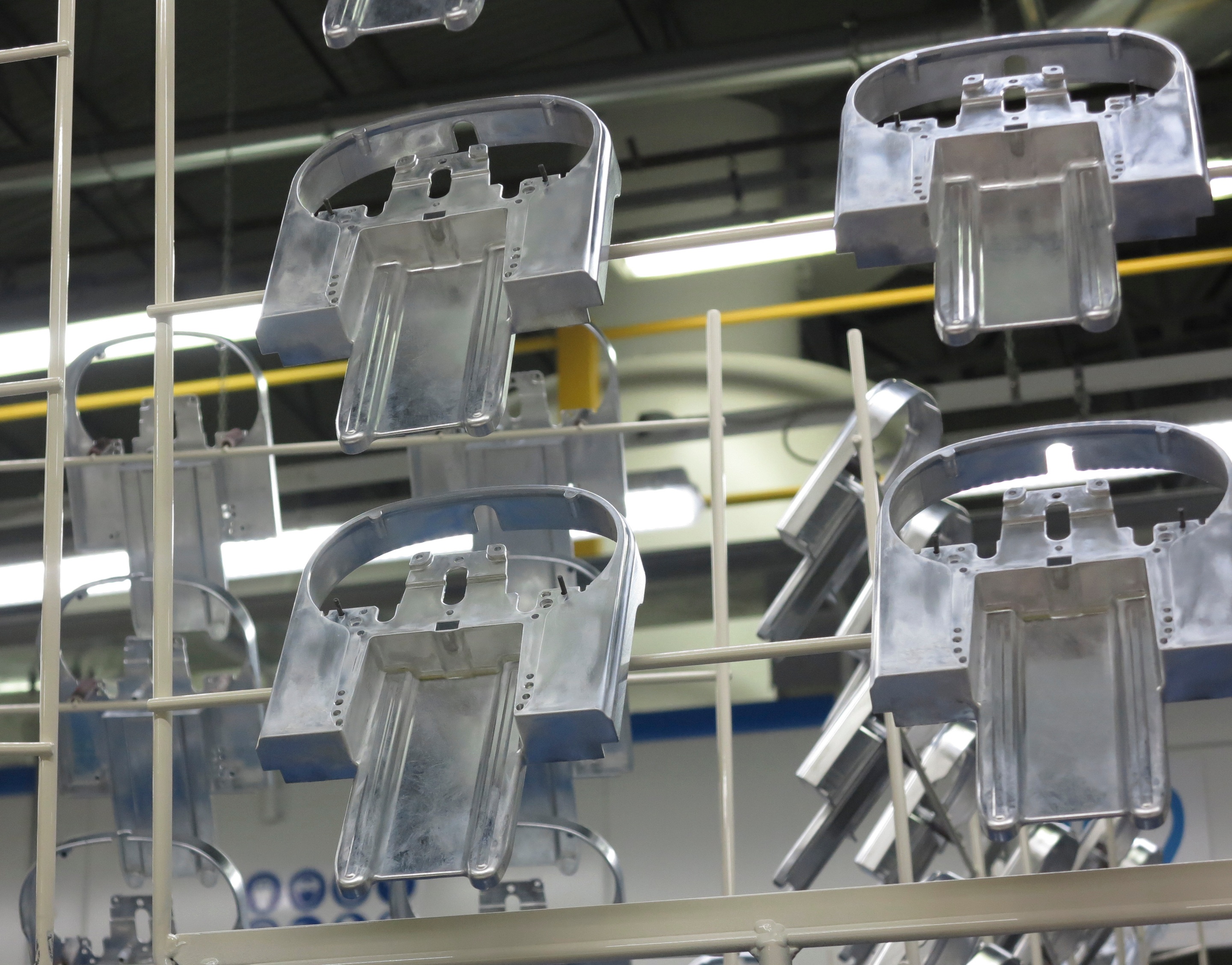
Die Casting Surface Treatments Avoiding Blisters Pitting And Other Defects In Plating

Reducing Die Soldering By Proper Use Of Lubricants

Gas Porosity And Surface Die Casting Defects

On The Tensile Failure Induced By Defect Band In High Pressure Die Casting Of Am60b Magnesium Alloy Sciencedirect
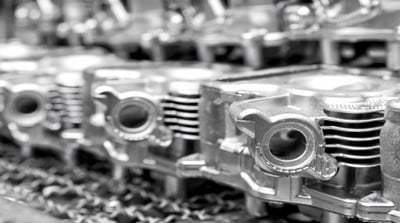
21 Casting Defects And How To Prevent Them In Your Products

An Example Of A Cold Shut Defect Brake Caliper Casting Produced During Download Scientific Diagram

Cast Aluminum Solutions Advantages Of Aluminum Alloy Casting And Defects A It Cast Aluminium Alloy Aluminum
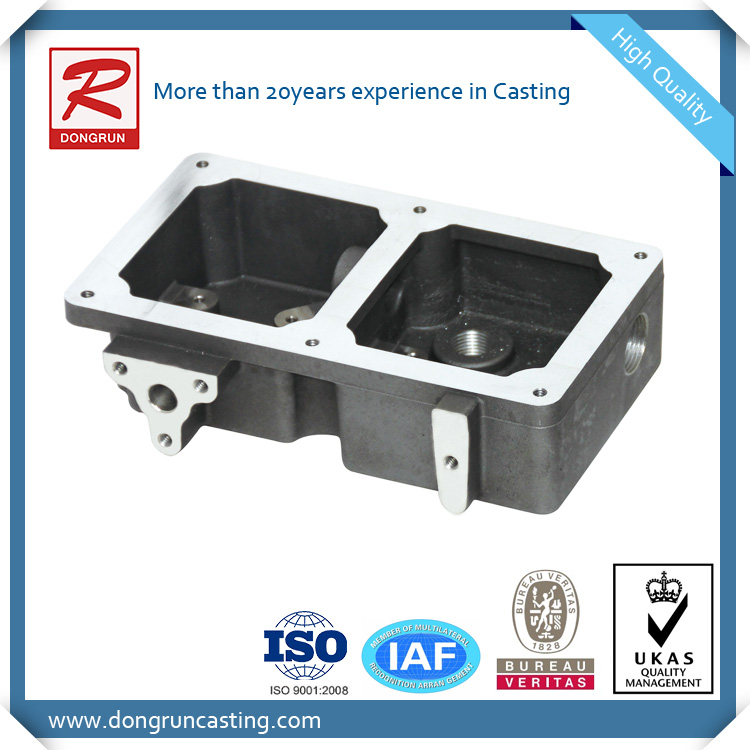
Common Defects Of Aluminum Castings
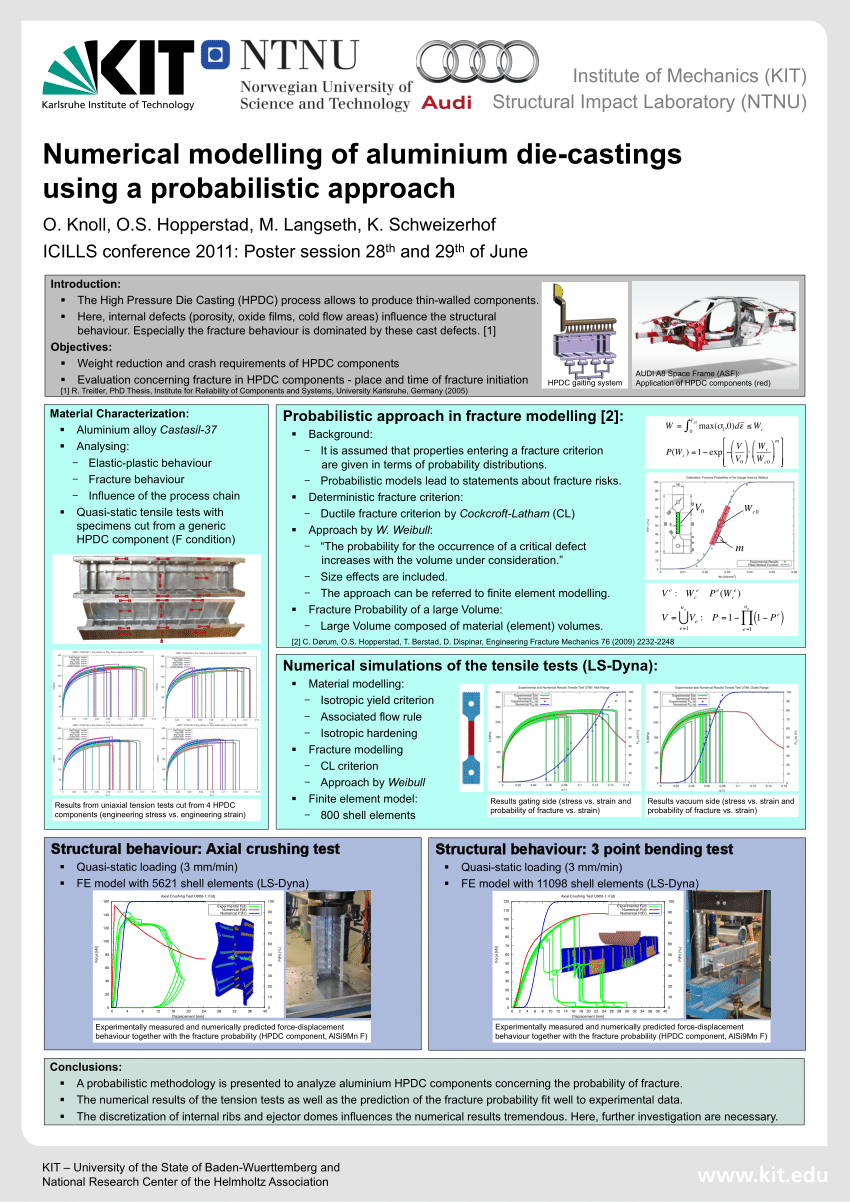
Pdf Numerical Modelling Of Aluminium Die Castings Using A Probabilistic Approach

Direct Chill Casting Total Materia Article
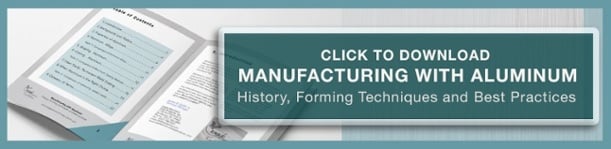
Casting Aluminum Comparison Of Methods
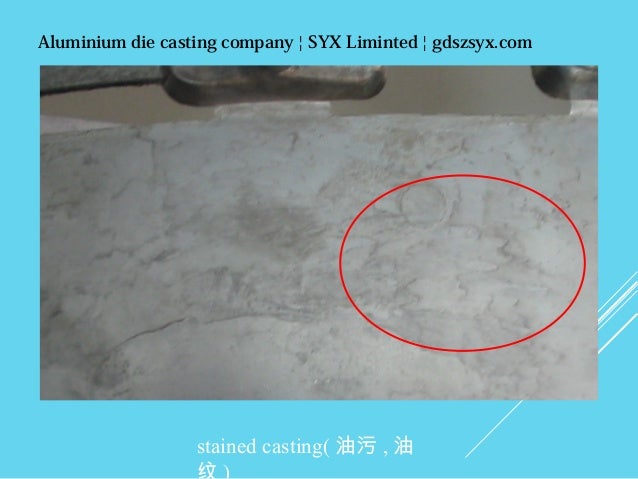
Aluminum Die Casting Defects

Forschungszentrum Julich Topics Aluminium Cast Alloys For High Performance Pistons

Free Evaluation Of Your Aluminum Castings Evaluate Quality Level Of Your Castings Or A Casting Problem
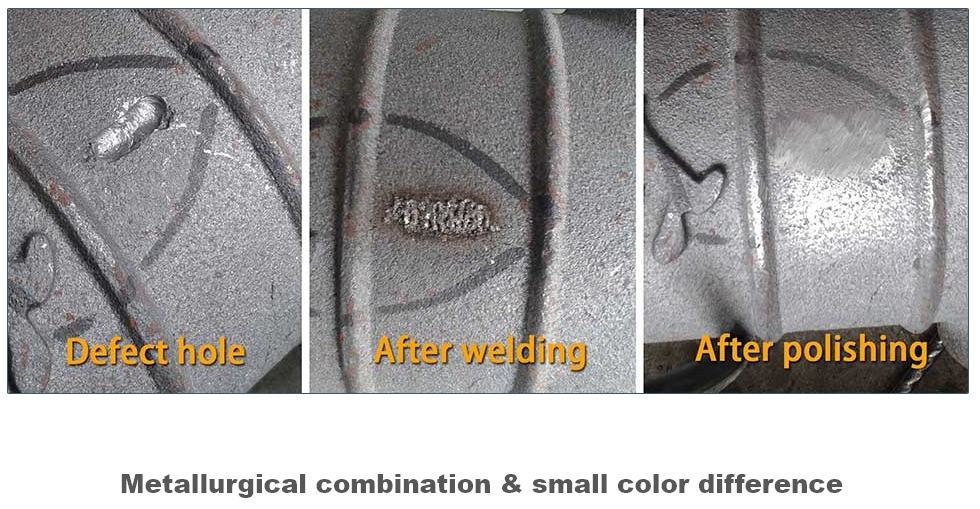
How To Repair Your Casting Defect Use Atomwelding Machine Foundry Solutions
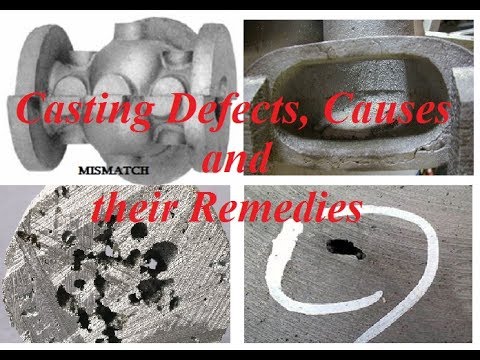
Casting Defects Causes Their Remedies Shrinkage Blow Holes Warpage Core Shift Fins Youtube

Marriage Casting Aluminum

Aluminium Casting Method Comparison Pros And Cons Of Different Casting Methods For Aluminium Parts Alteams Aluminium Casting Method Comparison Production Volume Matters
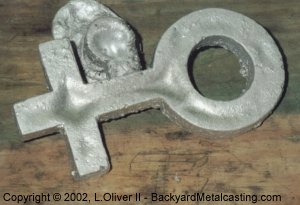
Prevent Casting Defects Backyardmetalcasting Com

Casting Metalworking Wikipedia
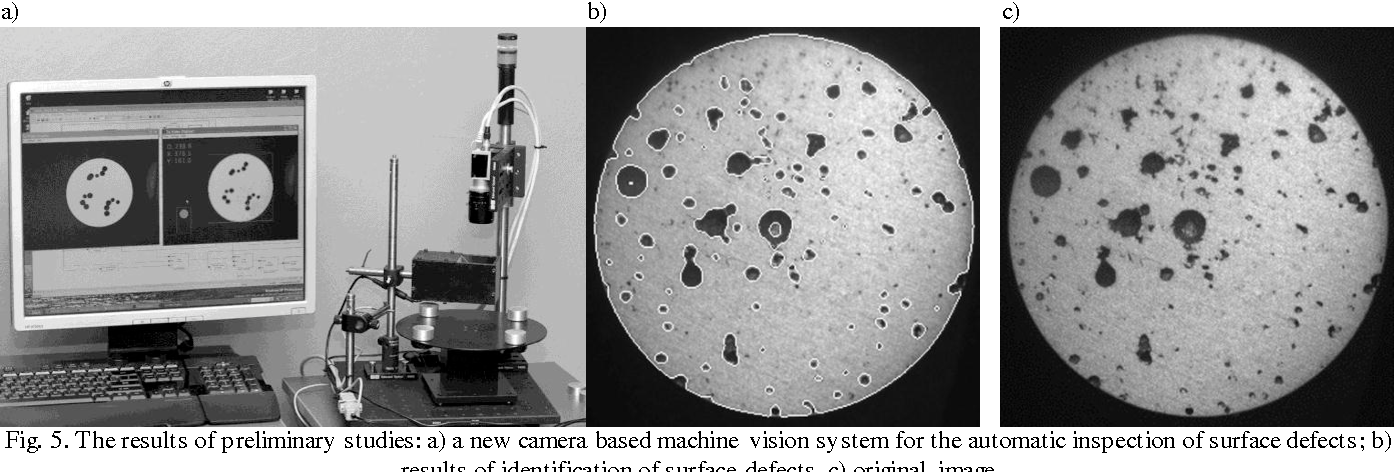
Pdf Automatic Inspection Of Surface Defects In Die Castings After Machining Semantic Scholar
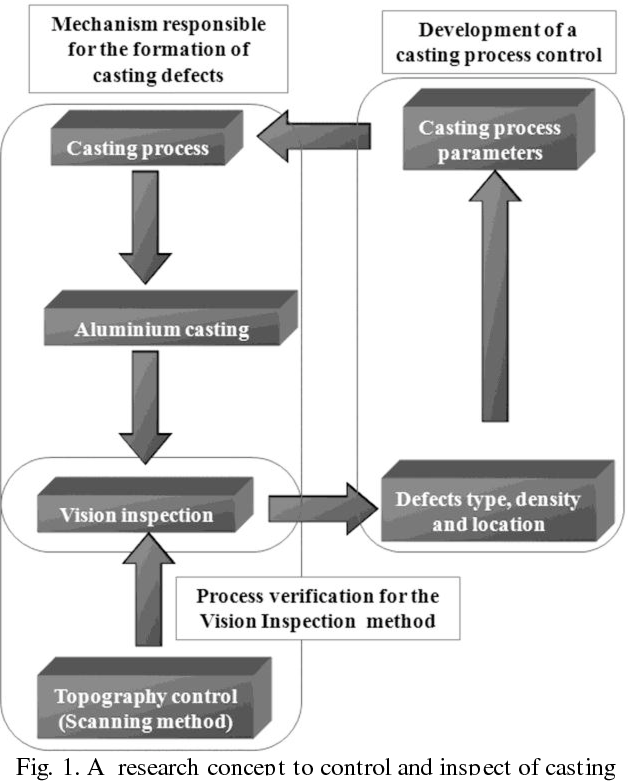
Pdf Advanced Metrology Of Surface Defects Measurement For Aluminum Die Casting Semantic Scholar
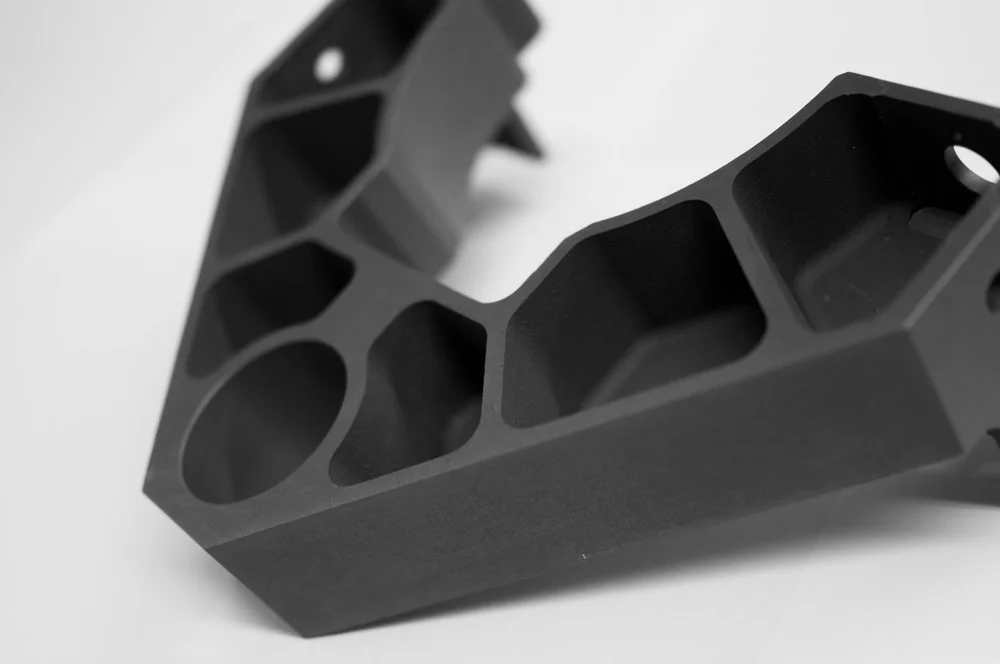
Casting Defects And How To Prevent Them Part 2 Haworth Castings Uk Aluminium Sand Castings And Gravity Die Castings Foundry
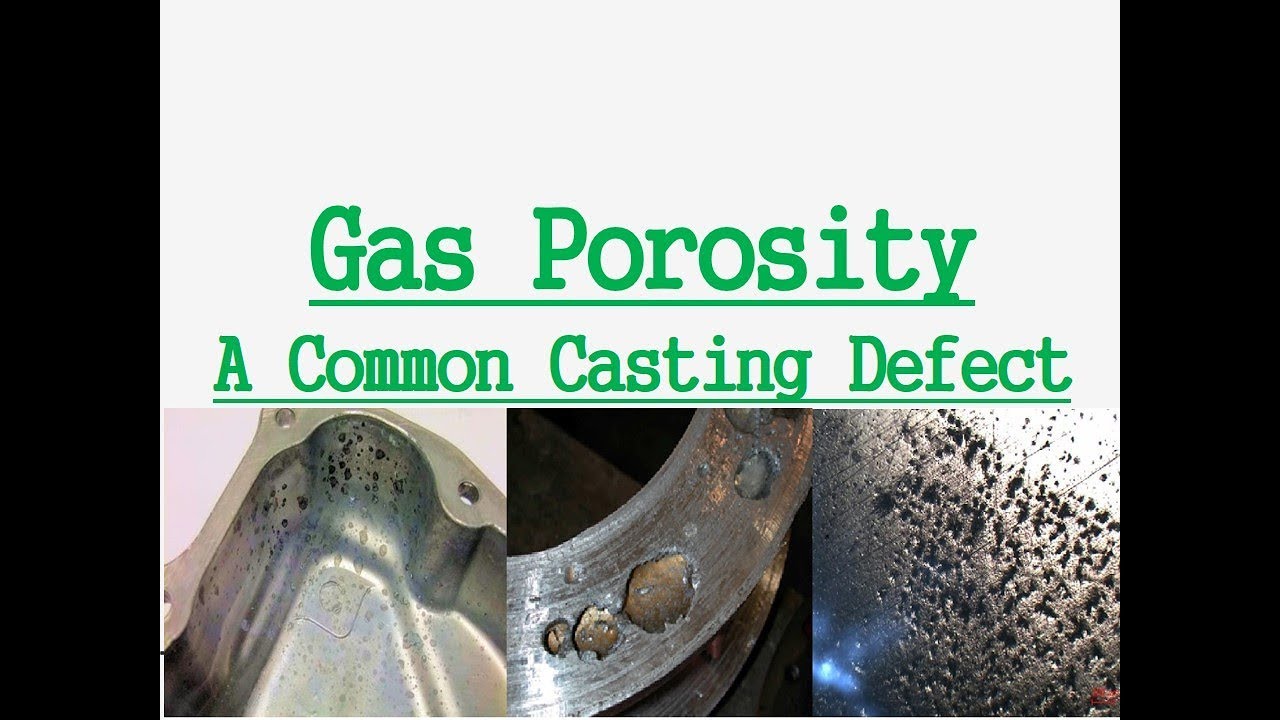
Gas Porosity Casting Defect Blow Holes Pin Holes Oxygen Nitrogen Hydrogen Youtube
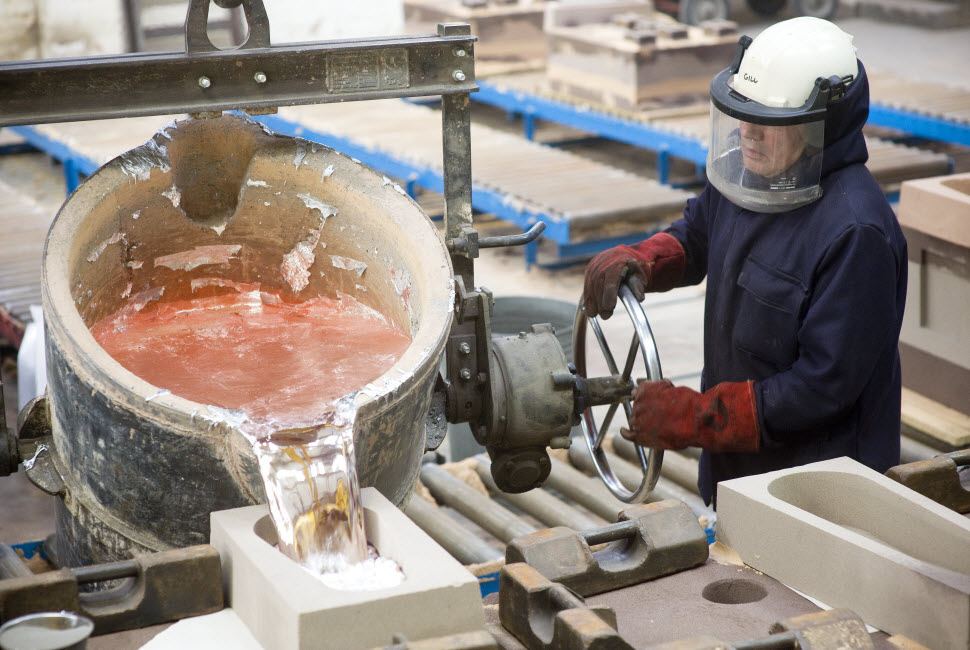
5 Types Of Aluminium Casting Defects And How To Treat Them
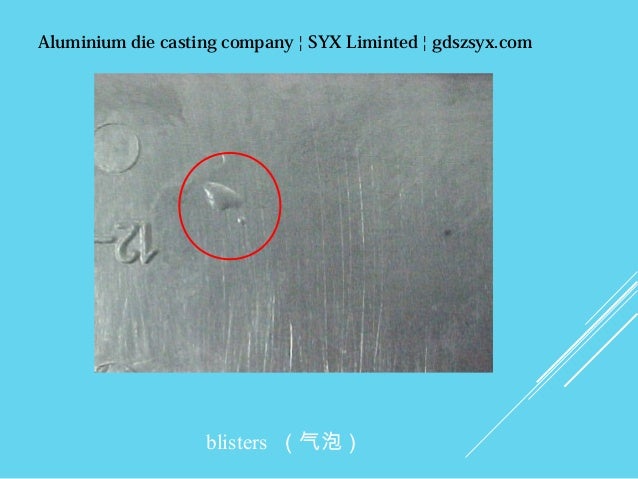
Aluminum Die Casting Defects

Influence Of Surface And Internal Casting Defects On The Fatigue Behaviour Of A357 T6 Cast Aluminium Alloy Sciencedirect

Sand Casting Defects Aluminium Casting Defects Steel Casting Defects Blogmech

How To Repair Casting Defects By Welding Solutions Fonderie

Casting Defect An Overview Sciencedirect Topics
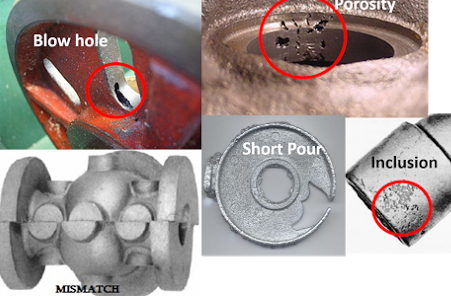
Types Of Casting Defects Bajrang Engineering

Prediction Of Shrinkage Defects During Investment Casting Process
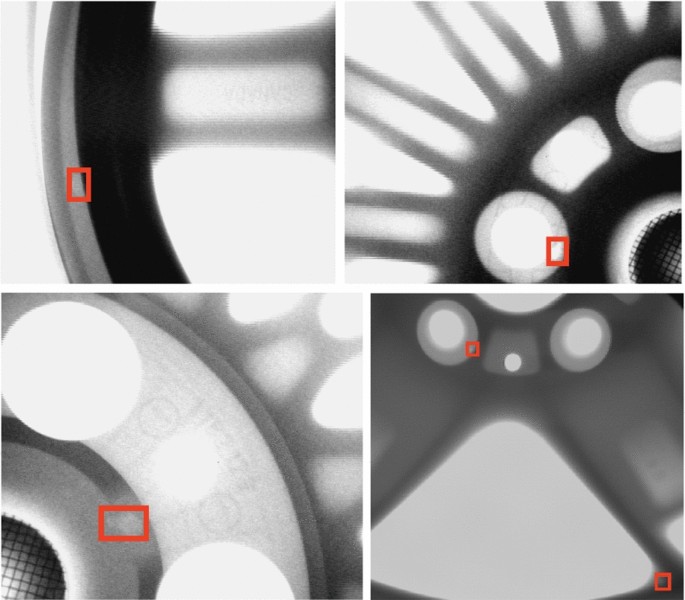
Aluminum Casting Inspection Using Deep Learning A Method Based On Convolutional Neural Networks Springerlink
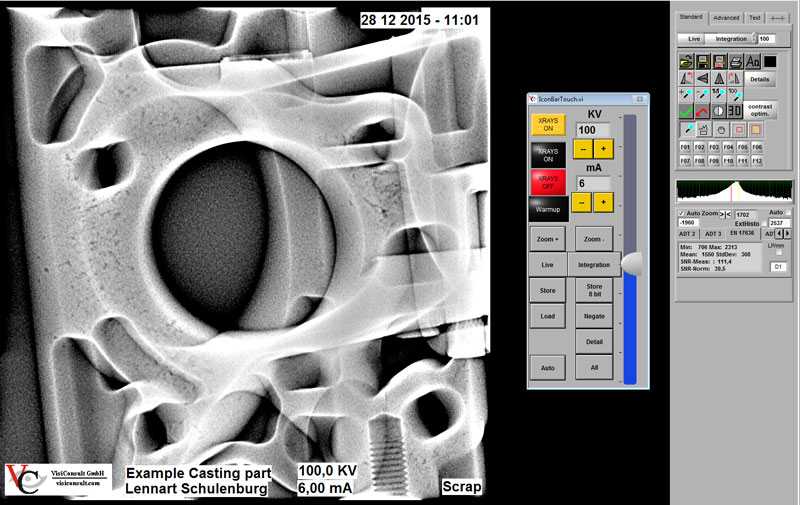
Aluminum Casting Al X Ray Inspection

Defects In Casting Its Causes Engineer S Academy Youtube
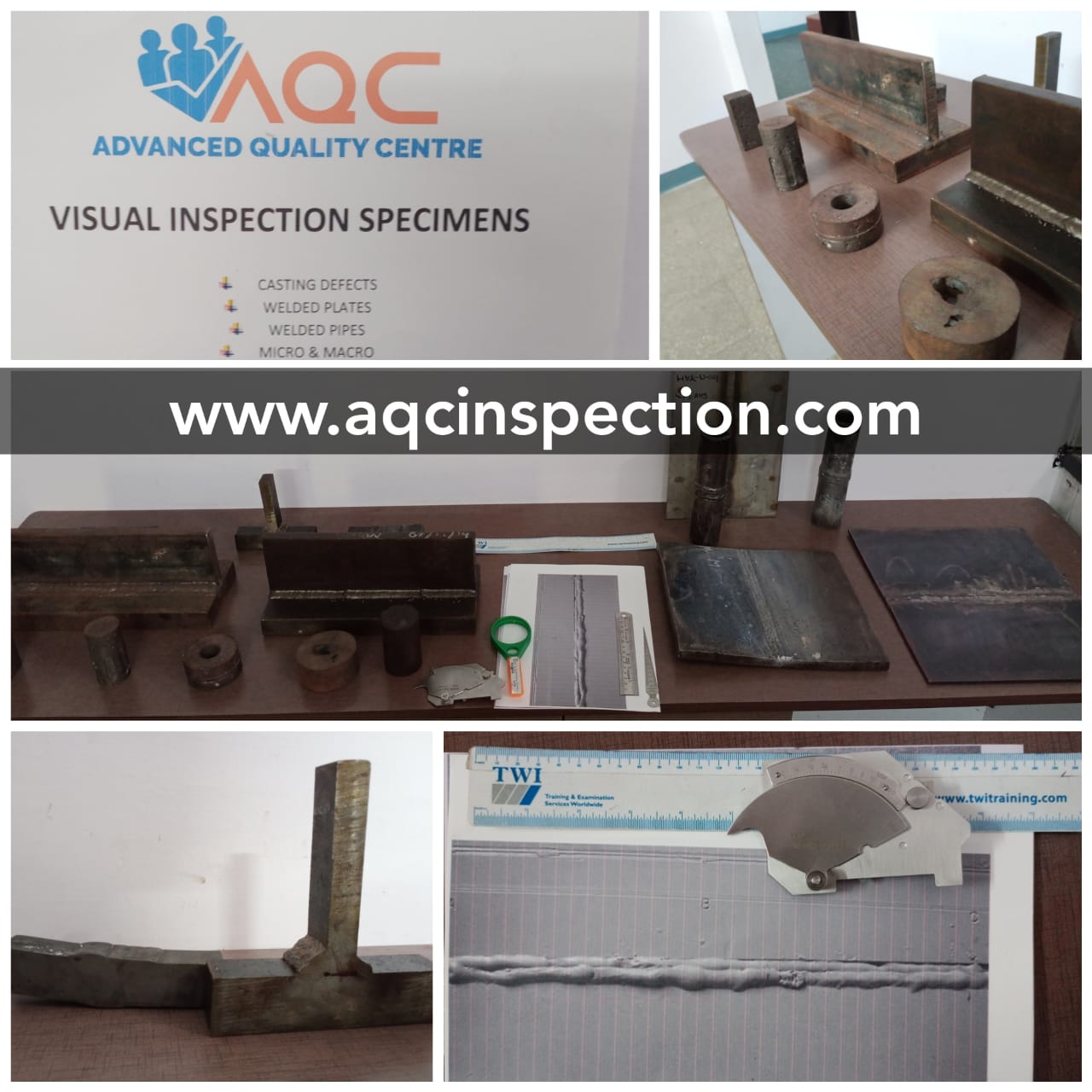
Ndt For Castings Onestopndt

Die Casting Defect And Solutions Oeform Die Casting Company
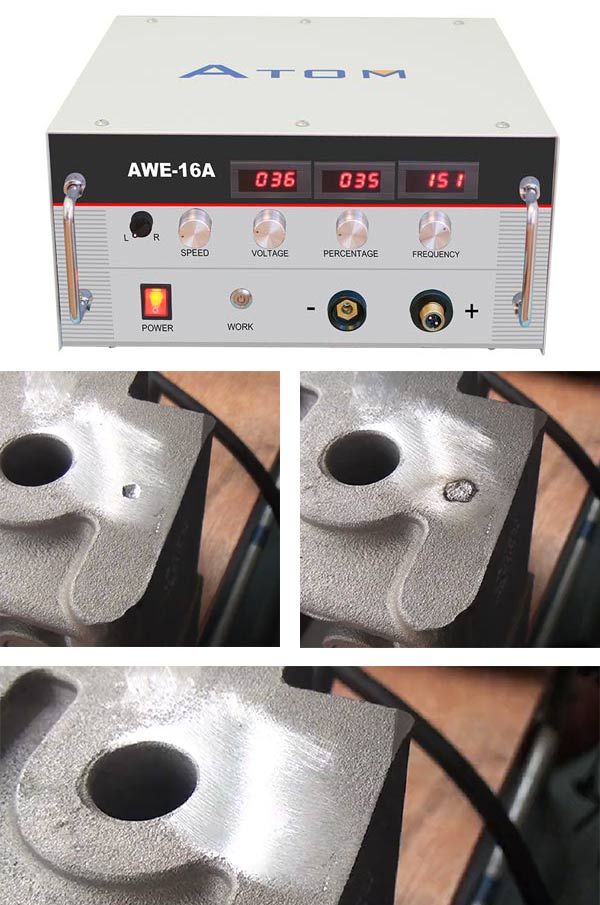
Aluminium Casting Defect Hole Welding Machine Cold Welding Machine Awe 16a Qingdao Atom Welding Equipments Co Ltd

Die Casting Defects How To Avoid Die Casting Defects

Reduce Blisters By Proper Application Of Die Casting Lubricants
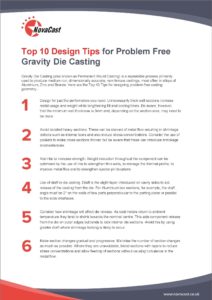
Top 10 Tips For Problem Free Gravity Die Casting Novacast

Die Casting Problems

Characterization Of Casting Defects In Aluminium Alloys Scientific Net
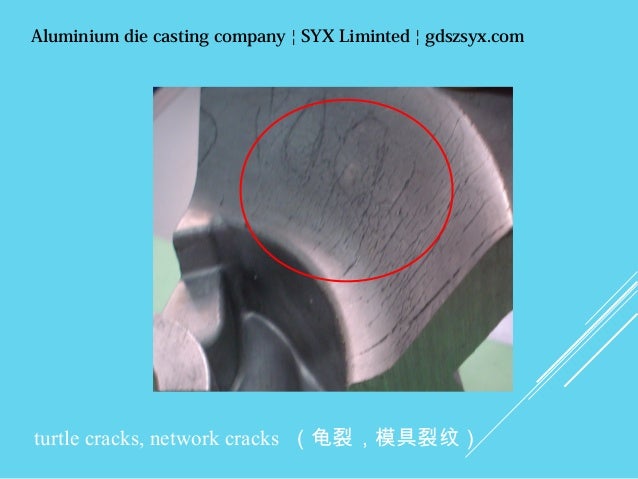
Aluminum Die Casting Defects

Sand Casting Defects Aluminium Casting Defects Steel Casting Defects Blogmech
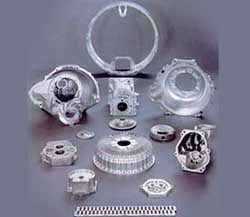
Aluminum Die Casting Defects And Remedies

Nadca Video News Die Casting Defects Inclusions Leakers And Cracks